DIY Custom T-Shirts are more than just a fashion statement—they’re a fun and creative way to express yourself. Whether you’re looking to wear your favorite quote, create a unique design for an event, or even start a small business, making your own t-shirts can be incredibly rewarding. In this guide, I’ll walk you through everything you need to know to get started on your custom t-shirt journey, from the tools and materials you will need sophisticated skills that can bring your creative output to a higher stage. So, let’s dive in!
Why Create Your Own DIY Custom T-Shirts?
Have you ever walked into a store and just couldn’t find the perfect shirt that speaks to you? Or maybe you wanted to wear something that reflects your personality or beliefs but couldn’t find it on the shelves? That’s exactly why I started creating my own t-shirts. The freedom to design something that’s 100% you is exhilarating. Not to mention, it’s often much cheaper than buying pre-made custom shirts.
Beyond just the cost savings, there’s something deeply satisfying about wearing a t-shirt you designed and made yourself. It’s a conversation starter, a confidence booster, and, for some of us, a great way to relieve stress. Creating your own t-shirts allows you to express your creativity in a practical, wearable way, and who doesn’t love a unique piece of clothing that nobody else has?
Essential Tools and Materials – DIY Custom T-Shirts
Before you start crafting your custom tees, you’ll need a few basic tools and materials. Don’t worry—you don’t need a fully equipped workshop to get started. Here’s a simple list to get you going:
Basic Materials You’ll Need:
- Plain T-shirts: Start with high-quality, blank t-shirts. Cotton is a popular choice because it’s breathable and takes well to most transfer methods.
- Fabric Paint or Markers: Great for hand-drawn designs and adding personal touches.
- Heat Transfer Vinyl (HTV): Perfect for bold, graphic designs. It’s a type of vinyl that you can cut into shapes or letters and then heat press onto your shirt.
- Transfer Paper: Ideal for more detailed designs or images. You print your design onto the paper and then transfer it to your t-shirt using heat.
Tools You’ll Need:
- Iron or Heat Press: For applying HTV or transfer paper designs. An iron works for beginners, but a heat press provides more even heat and pressure.
- Cutting Machine (e.g., Cricut or Silhouette): If you’re using HTV or want to create precise stencils, a cutting machine is invaluable.
- Scissors and X-Acto Knife: Handy for cutting out stencils or making minor adjustments.
When I first started, I didn’t have a fancy cutting machine or a heat press. I used a regular iron, some printable transfer paper, and a pair of scissors. And you know what? It worked just fine! So don’t worry if you’re just starting out with the basics—you can always upgrade your tools as you go.
Choosing Your Design: Tips for Beginners and Pros – DIY Custom T-Shirts
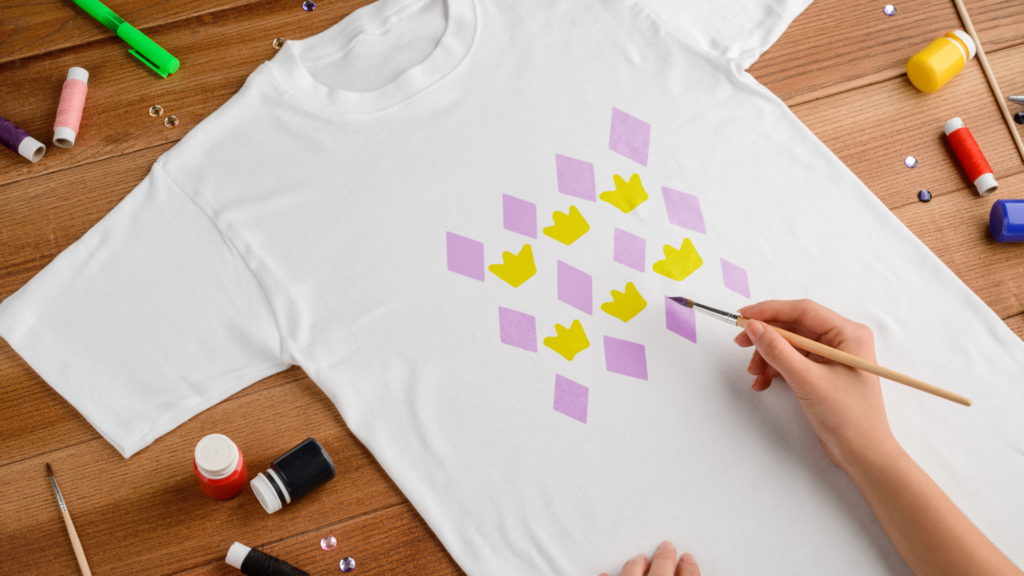
Designing your t-shirt is the fun part, but it can also be a little intimidating if you’re not sure where to start. Here are some tips to help you choose a design that’s perfect for you:
Finding Inspiration:
I often find inspiration on Pinterest or Instagram. There’s a whole world of creative ideas out there, from minimalist designs and typography to complex graphics and photo transfers. Start by pinning or saving designs you like. Over time, you’ll start to see a pattern in what catches your eye.
Creating Your Own Designs:
If you’re comfortable with design software like Adobe Illustrator or Canva, you can create your own designs from scratch. For those just starting out, Canva is incredibly user-friendly and offers tons of templates that you can customize.
When I was a beginner, I loved using Canva because it made designing so approachable. I didn’t need any design skills, just a good eye for what I liked. After a few tries, I started feeling more confident and even began experimenting with my own hand-drawn designs, which I later transferred using fabric paint.
Design Considerations:
- Keep It Simple: Especially if you’re new to this, simpler designs are easier to execute and often look cleaner.
- Use Bold, Contrasting Colors: These stand out more on fabric and are easier to see from a distance.
- Think About Placement: Common placements are on the chest or back, but you can get creative with side designs or sleeve prints.
Step-by-Step Guide to Creating Your DIY Custom T-Shirts
Now that you’ve got your materials and design, it’s time to bring your vision to life! Here’s a step-by-step guide to making your custom t-shirts.
Step 1: Prepare Your Workspace
Set out a smooth and flat surface and gather all of your materials. Make sure your t-shirt is clean and free of wrinkles. This will help ensure a smooth transfer of your design.
Step 2: Create Your Stencil or Cut Your Vinyl
If you’re using a cutting machine, load your design into the machine’s software and let it cut your vinyl or stencil material. If you’re using transfer paper, print your design according to the package instructions.
When I first tried using HTV, I didn’t have a cutting machine, so I printed out a stencil on regular paper and carefully cut it out with an X-Acto knife. It was tedious, but it worked! So, don’t let a lack of tools stop you from getting started.
Step 3: Apply the Design to the T-Shirt
Place your stencil or vinyl on the shirt where you want the design to appear. If you’re using fabric paint, carefully paint within your stencil. For HTV, lay your vinyl with the shiny side up.
Step 4: Set the Design with Heat
This is where the magic happens! Using an iron or heat press, apply even pressure to the design area. Make sure to follow the specific heat and time settings for the material you’re using. For HTV, this is usually around 300-320°F for about 15-20 seconds. Don’t forget to use a protective sheet like parchment paper between the iron and the vinyl to prevent sticking.
Step 5: Finishing Touches
After you’ve applied your design, let it cool slightly before peeling off the backing. When using fabric paint, please let it dry thoroughly. Once your design is set and dry, your custom t-shirt is ready to wear!
Advanced Techniques for DIY Custom T-Shirts
Once you’ve mastered the basics, there are plenty of ways to take your t-shirts to the next level.
Screen Printing
Screen printing is a fantastic method for making multiple shirts with the same design. It involves creating a stencil (or “screen”) and using it to apply layers of ink onto the shirt. It’s a bit more involved than the other methods but offers professional-quality results.
Dye Sublimation
This technique uses heat to transfer dye directly into the fabric, creating vibrant, full-color designs that are incredibly durable. However, it requires a special printer and sublimation ink, making it a bit more costly to get started.
Adding Embellishments
Consider adding embellishments like beads, sequins, or embroidery to give your t-shirt a unique touch. I once made a t-shirt for a friend’s birthday and added little fabric flowers around the neckline. She loved it, and it was a great way to personalize the gift!
Common Mistakes and How to Avoid Them – DIY Custom T-Shirts
Even the most seasoned DIY enthusiasts make mistakes. The following are some typical traps and ways to prevent them:
- Using the Wrong Heat Settings: Too much heat can cause vinyl to melt or paint to crack. Always follow the recommended settings for your materials.
- Not Testing Your Design: Before applying a design to your final t-shirt, test it on a scrap piece of fabric. This will help you visualize the appearance of the colors involved and how the fabric responds to heat.
- Rushing the Process: Patience is key! Let each layer dry fully before adding another, and make sure to let heat-set designs cool properly.
Caring for Your DIY Custom T-Shirts
To ensure your custom creations last, it’s important to care for them properly.
Washing Tips:
- To protect the pattern, always turn your shirt inside out prior to washing.
- Use cold water and a gentle cycle.
- Avoid bleach or harsh detergents that can fade the design.
Drying Tips:
- Air dry your shirts when possible. If you have to use a dryer, please set the setting to a low temperature.
- Avoid ironing directly over the design; if needed, use a pressing cloth between the iron and the shirt.
Expanding Your DIY Custom T-Shirts Business
If you’ve caught the t-shirt-making bug, then why not turn it into a side hustle? Initially, you can start small by selling to friends and family. Alternatively, you could set up an online shop on platforms like Etsy or eBay. Additionally, social media is a fantastic tool for marketing your designs and building a customer base. For example, you can share your creations, engage with followers, and perhaps even run a few giveaways to get started!
Conclusion
Creating your own DIY custom t-shirts is a fun and rewarding DIY project that anyone can do, whether you’re a beginner or a seasoned pro. It’s a great way to express your personality, make unique gifts, or even start a small business. So, gather your materials, fire up your creativity, and get started on your first (or next) custom t-shirt today!
Happy crafting!
Check more of our Home Decor DIY ideas !
Join our Facebook Community for more informations!